Company Name | Contact Info | Location | ||||||||||||
---|---|---|---|---|---|---|---|---|---|---|---|---|---|---|
SHANDONG MINGHUNG OSB&MDF MACHINERY EQUIPMENT MANUFACTURING CO., LTD.
Machinery Industrial Park No.0191, Xiao Ge Zhuang Village, Yitang Town, Lanshan District, Linyi City, Shandong Province / / / CHINA
|
Contact Info: +86 187 6990 0191
|
Hall: 9
Stand: 905 E
|
||||||||||||
Product Groups | ||||||||||||||
|
- Company Info
- Products
- Represented Companies
- Company Brands
Our main products include Plywod production line (Wood debarking machine, Veneer peeling machine, Vacuum veneer stacker, Veneer dryer, Blade sharpener, Plywood assembly line, Core composer, Veneer patching machine, Cold press machine, Hot press machine, Glue spreader, Glue mixer, Plywood edge cutting machine, Sanding machine and calibrating machine, Lift table); Particle board production line /MDF production line /OSB production line such as Wood chipper, Rotary dryer, Screening machine, Glue blender, Mat former, Continuous pre-press, Multi-layers Hot press, Auto cutting machine, Sanding machine and so on
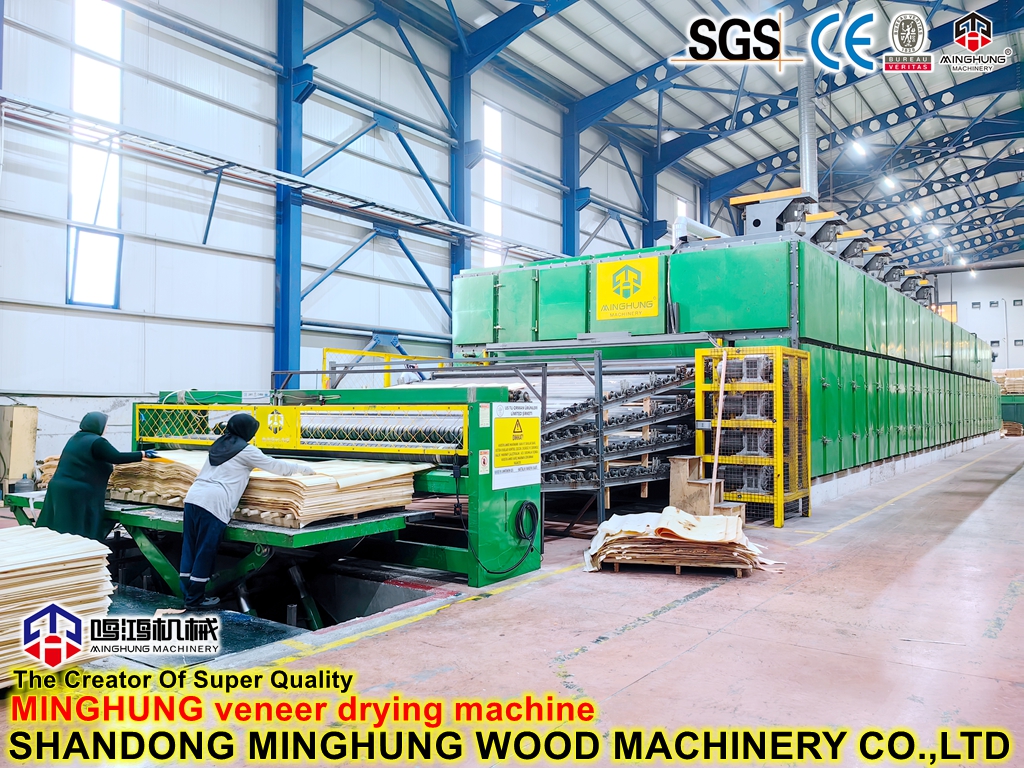
Mesh Veneer Drying Machine: The Perfect Balance of Airflow and Support One of the most popular options in the market is the mesh veneer drying machine. This type of machine utilizes a mesh conveyor belt to transport the veneer sheets through the drying chamber. The mesh design allows for excellent airflow, ensuring uniform drying throughout the entire veneer stack. Additionally, the mesh provides adequate support to prevent any warping or deformation of the veneer during the drying process. Roller Veneer Drying Machine: Ideal for High-Volume Production For woodworking businesses with high production demands, a roller veneer drying machine is the perfect choice. This machine utilizes a series of rollers to transport the veneer sheets through the drying chamber. The rollers ensure smooth and continuous movement, allowing for efficient drying of large quantities of veneer. With multiple layers available, ranging from 1 to 6 layers, these machines can handle a wide range of production volumes. Wire Veneer Dryer: Precision Drying for Thin Veneers When it comes to drying thin veneers, a wire veneer dryer is the go-to option. This machine utilizes a series of parallel wires to support the veneer sheets during the drying process. The wires allow for maximum airflow, ensuring quick and precise drying of the thin veneers. With various width options available, including 2800MM, 3200MM, 4000MM, 4500MM, 4800MM, and 5000MM, these machines can accommodate different sizes of veneer sheets.
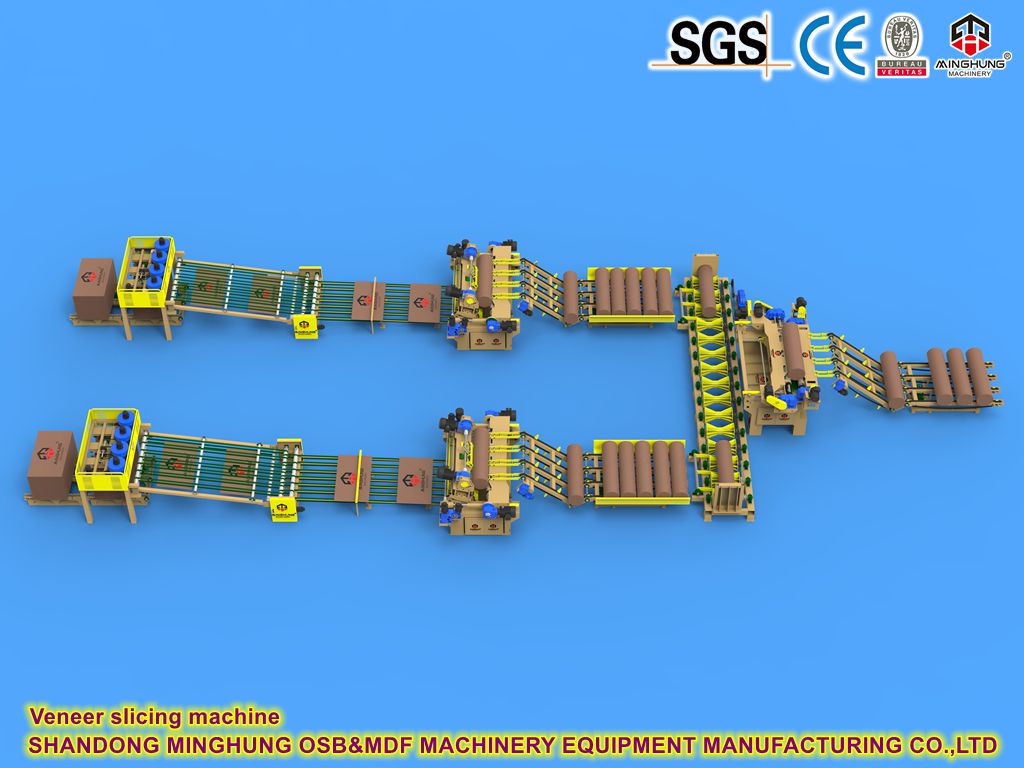
Enhancing Efficiency with an Automatic Veneer Peeling Machine Line In today s fast-paced woodworking industry, the demand for high-quality veneer products is on the rise. To meet this demand, manufacturers are constantly seeking ways to improve efficiency and productivity. One solution that has gained significant popularity is the Automatic Veneer Peeling Machine Line. This comprehensive line includes several essential components, such as a log conveyor, log debarker, veneer peeling machine, and veneer stacker machine. With lengths ranging from 1500MM to 4000MM, this line is designed to handle logs with diameters ranging from 200mm to 700mm. Moreover, it can produce veneer with a thickness ranging from 0.3mm to 4mm. The log conveyor serves as the initial stage of the process, efficiently transporting logs to the next stage. By automating this step, manufacturers can save valuable time and reduce manual labor. This not only increases productivity but also minimizes the risk of injuries associated with manual log handling. The log debarker is a crucial component that removes the bark from the logs before they enter the peeling machine. By eliminating the need for manual debarking, this machine ensures a clean and smooth surface for the subsequent peeling process. This, in turn, enhances the quality of the veneer produced. The heart of the Automatic Veneer Peeling Machine Line is the veneer peeling machine itself. Equipped with advanced technology, this machine is capable of peeling logs with precision and consistency. Its adjustable settings allow manufacturers to produce veneer of varying thicknesses, catering to the specific requirements of different projects. This versatility is a significant advantage, as it enables manufacturers to meet the diverse needs of their customers. Once the veneer is peeled, the veneer stacker machine comes into play. This machine neatly stacks the veneer sheets, ensuring easy handling and transportation. By automating this process, manufacturers can streamline their operations and reduce the risk of damage to the delicate veneer sheets. The Automatic Veneer Peeling Machine Line offers numerous benefits to manufacturers. Firstly, it significantly improves efficiency by automating various stages of the veneer production process. This, in turn, leads to increased productivity and reduced labor costs. Additionally, the line s ability to handle logs of different sizes and produce veneer with varying thicknesses makes it a versatile choice for manufacturers with diverse product requirements. In conclusion, the Automatic Veneer Peeling Machine Line is a game-changer in the woodworking industry. Its ability to streamline operations, increase productivity, and produce high-quality veneer makes it an invaluable asset for manufacturers. By investing in this advanced technology, manufacturers can stay ahead of the competition and meet the growing demand for top-notch veneer products.
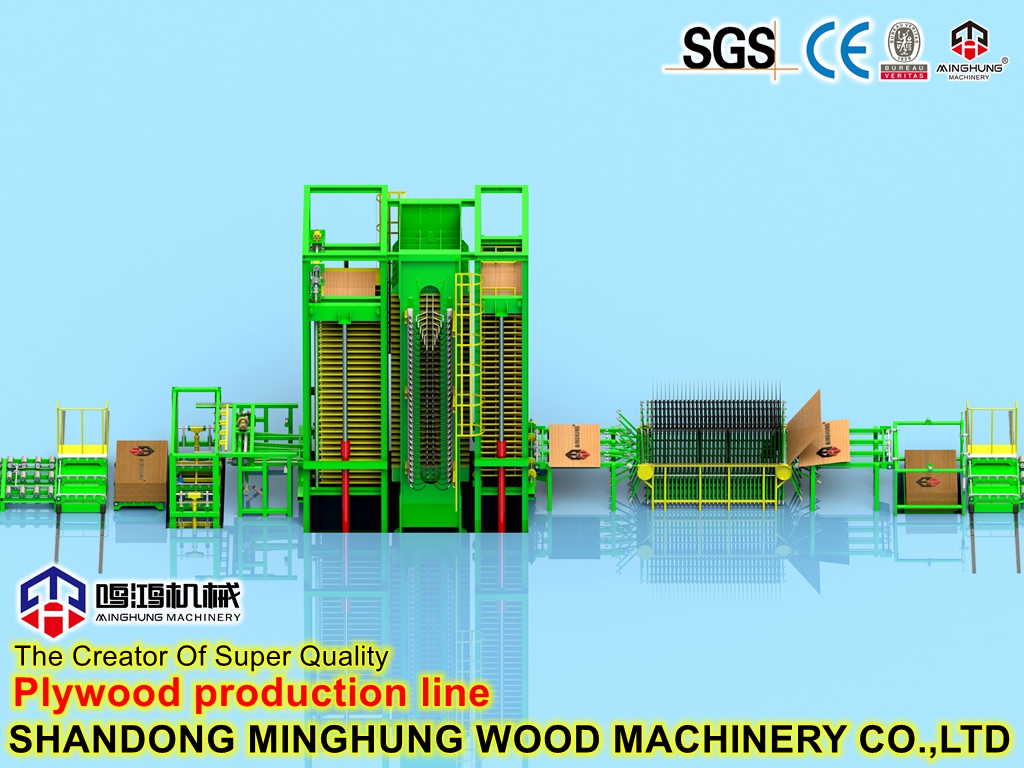
nhancing Plywood Hot Press Machine Efficiency with Auto Loader and Unloader Introduction: The plywood manufacturing industry has witnessed significant advancements in recent years, with automation playing a crucial role in improving efficiency and productivity. One such innovation is the auto loader and unloader for plywood hot press machines. This article explores how this technology can revolutionize the plywood production process, enhancing work efficiency, increasing production capacity, and reducing labor costs. Streamlining the Plywood Hot Press Process: Traditionally, the plywood hot press process involved manual labor, requiring workers to load and unload the plywood sheets onto the press machine. This labor-intensive process often led to inefficiencies, slower production rates, and increased labor costs. However, with the introduction of auto loader and unloader systems, these challenges are effectively addressed. Improved Work Efficiency: The auto loader and unloader for plywood hot press machines eliminate the need for manual labor during the pressing process. This automation ensures a seamless and continuous operation, significantly improving work efficiency. With the ability to load and unload plywood sheets automatically, the machine can operate at optimal speed without interruptions, leading to higher productivity levels. Increased Production Capacity: By eliminating the dependency on manual labor, the auto loader and unloader systems enable plywood manufacturers to increase their production capacity. The consistent and uninterrupted operation of the hot press machine allows for a higher number of plywood sheets to be processed within a given timeframe. This increased production capacity translates into higher output and greater profitability for plywood manufacturers. Labor Cost Savings: One of the most significant advantages of implementing auto loader and unloader systems is the substantial reduction in labor costs. With the automation of the loading and unloading process, the need for manual labor is eliminated. This not only reduces the number of workers required but also eliminates the associated costs such as wages, benefits, and training. The savings generated from reduced labor costs can be reinvested into other areas of the business, further enhancing overall profitability. Enhanced Safety and Quality: Apart from improving efficiency and reducing labor costs, auto loader and unloader systems also contribute to enhanced safety and product quality. With the elimination of manual handling, the risk of accidents and injuries is significantly reduced. Additionally, the automation ensures precise and consistent loading and unloading, resulting in higher quality plywood products. Conclusion: The implementation of auto loader and unloader systems for plywood hot press machines offers numerous benefits to plywood manufacturers. By improving work efficiency, increasing production capacity, and reducing labor costs, this technology revolutionizes the plywood production process. Furthermore, the enhanced safety and product quality contribute to the overall success and profitability of the business. Embracing automation in the plywood industry is a step towards staying competitive in a rapidly evolving market.
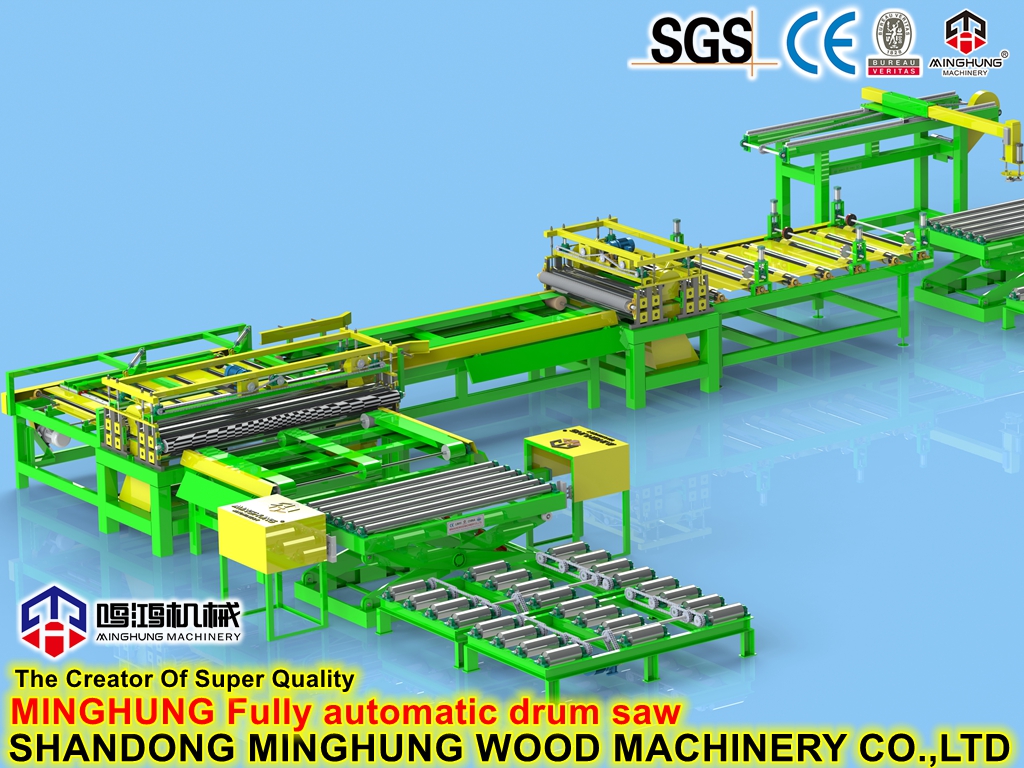
In the ever-evolving woodworking industry, efficiency and precision are key factors that determine success. With the introduction of the Automatic Plywood Trimming Saw Machine Line, manufacturers can now achieve both in a seamless and automated manner. This cutting-edge machinery offers adjustable speed, automatic loading, and stacking capabilities, revolutionizing the plywood trimming process. One of the standout features of the Automatic Plywood Trimming Saw Machine Line is its ability to cut plywood to precise dimensions. With a cutting width range of 600mm to 1900mm and a cutting length range of 1500mm to 3200mm, this machine ensures that plywood is tailored to meet specific requirements. Whether it s for furniture, construction, or other applications, the flexibility in size allows manufacturers to cater to diverse customer needs. Moreover, the Automatic Plywood Trimming Saw Machine Line accommodates plywood thicknesses ranging from 3mm to 70mm. This wide range enables manufacturers to work with various plywood grades, ensuring versatility in production. Whether it s thin sheets for intricate designs or thicker panels for structural purposes, this machine can handle it all with precision and accuracy. The adjustable speed feature of the Automatic Plywood Trimming Saw Machine Line further enhances its efficiency. Manufacturers can adapt the cutting speed to suit different plywood types and thicknesses, optimizing productivity without compromising on quality. This adaptability ensures that the machine can handle a wide range of projects, from high-volume production to intricate custom orders. Another notable advantage of this machine line is its automatic loading and stacking capabilities. By eliminating the need for manual handling, manufacturers can significantly reduce labor costs and minimize the risk of injuries. The automated system seamlessly loads plywood onto the machine and stacks the trimmed pieces, streamlining the entire production process. In addition to its efficiency and automation, the Automatic Plywood Trimming Saw Machine Line also prioritizes safety. Equipped with advanced safety features, such as emergency stop buttons and protective barriers, it ensures a secure working environment for operators. This focus on safety not only protects workers but also prevents potential damage to the machinery and the plywood itself. In conclusion, the Automatic Plywood Trimming Saw Machine Line is a game-changer in the woodworking industry. Its adjustable speed, automatic loading, and stacking capabilities, combined with the ability to cut plywood to precise dimensions, make it an invaluable asset for manufacturers. With its wide range of plywood thicknesses and advanced safety features, this machine line offers enhanced efficiency, productivity, and quality. Embrace this cutting-edge technology to stay ahead in the competitive woodworking market.
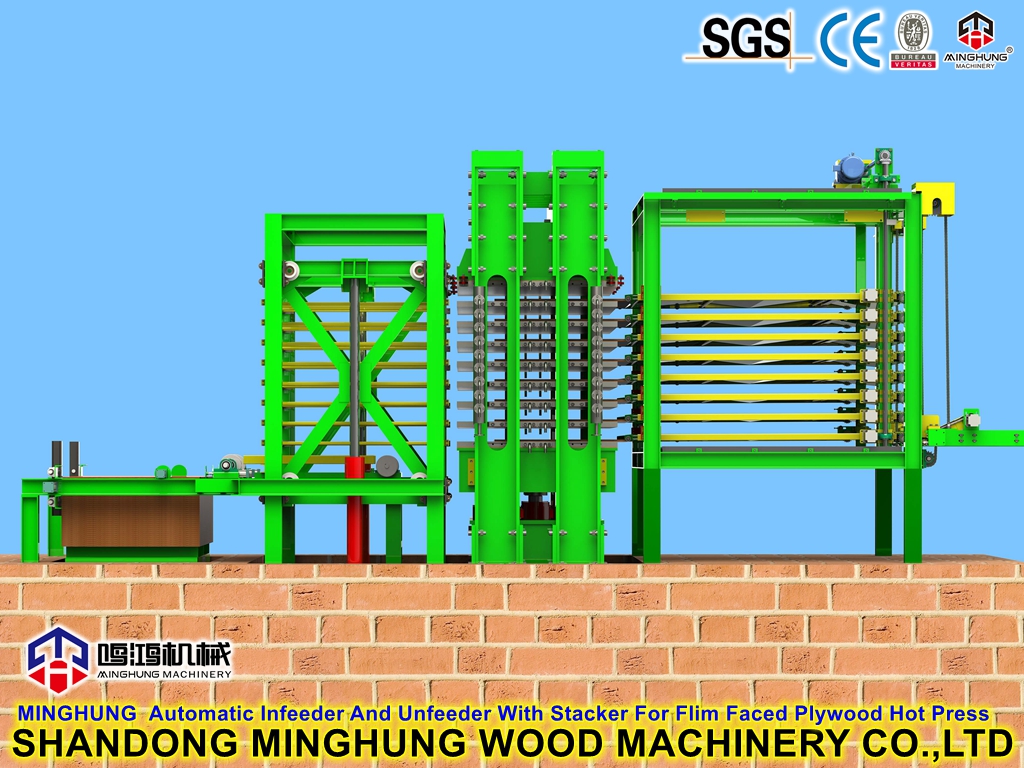
Introduction: Film faced plywood is a popular choice in the construction and furniture industries due to its durability and versatility. However, the production process can be time-consuming and labor-intensive. To address this challenge, manufacturers have turned to automated solutions such as automatic infeeders. In this article, we will explore the benefits and functionalities of automatic infeeders for film faced plywood production. Enhancing Efficiency: One of the primary advantages of using automatic infeeders in film faced plywood production is the significant improvement in efficiency. These machines are designed to handle large volumes of plywood sheets, eliminating the need for manual handling. By automating the infeeding process, manufacturers can save time and reduce labor costs, resulting in higher overall productivity. Precise Sheet Alignment: Achieving precise sheet alignment is crucial in film faced plywood production to ensure consistent quality. Manual handling can often lead to misalignment, causing defects and wastage. Automatic infeeders, on the other hand, are equipped with advanced sensors and positioning systems that guarantee accurate sheet alignment. This not only enhances the quality of the final product but also minimizes material wastage, leading to cost savings. Versatile and Customizable: Automatic infeeders for film faced plywood are designed to accommodate various sheet sizes and thicknesses. This versatility allows manufacturers to produce a wide range of plywood products without the need for extensive reconfiguration or adjustments. Additionally, these machines can be customized to meet specific production requirements, further enhancing their flexibility and adaptability. Seamless Integration: Integration with existing production lines is a crucial consideration when implementing automated solutions. Automatic infeeders are designed to seamlessly integrate with other machinery, such as veneer cutters and gluing machines, ensuring a smooth and uninterrupted production flow. This integration not only reduces downtime but also eliminates potential bottlenecks, enabling manufacturers to meet production targets more efficiently. Improved Worker Safety: Manual handling of large and heavy plywood sheets can pose significant risks to workers, including musculoskeletal injuries. By automating the infeeding process, automatic infeeders eliminate the need for manual lifting and carrying, thereby reducing the risk of workplace accidents and injuries. Ensuring a safe working environment not only protects the well-being of employees but also minimizes downtime and associated costs. Conclusion: Automatic infeeders have revolutionized film faced plywood production by streamlining the infeeding process. With their ability to enhance efficiency, ensure precise sheet alignment, offer versatility and customization, seamlessly integrate with existing production lines, and improve worker safety, these machines have become an invaluable asset for manufacturers. By investing in automatic infeeders, film faced plywood producers can optimize their operations, increase productivity, and deliver high-quality products to meet market demands.
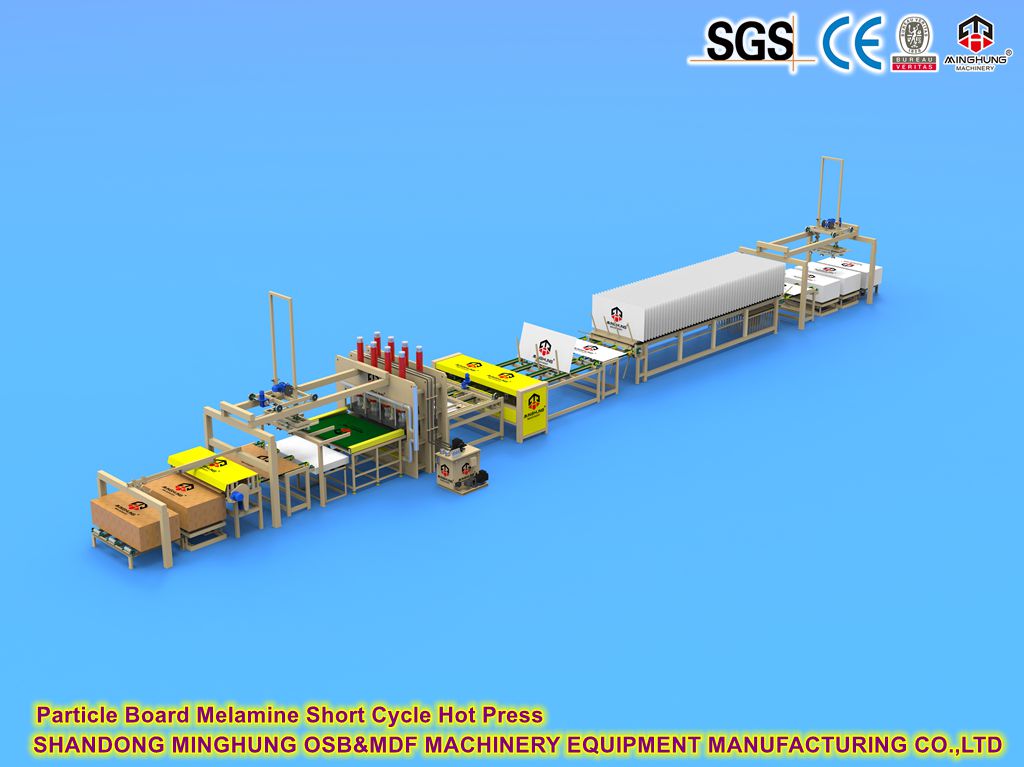
Mastering the Art of Laminating Melamine Paper on MDF, Particle Board, and Plywood Using Short Cycle Hot Press Machines Laminating melamine paper onto MDF, particle board, and plywood is a crucial process that requires precision and efficiency. Short cycle hot press machines have revolutionized this process, enabling faster production while maintaining high-quality results. The key to successful lamination lies in understanding the intricacies of the materials involved and the operation of the short cycle hot press machine. Melamine paper, known for its durability and aesthetic appeal, is applied to the substrate using heat and pressure to create a seamless bond. MDF, particle board, and plywood serve as the ideal substrates for melamine lamination due to their smooth surfaces and structural integrity. The short cycle hot press machine utilizes a combination of heat and pressure to activate the adhesive properties of the melamine paper, ensuring a strong and long-lasting bond. To achieve optimal results, it is essential to prepare the substrate by sanding it to create a smooth surface free of imperfections. The melamine paper should be carefully aligned and placed on the substrate before being fed into the hot press machine. The short cycle hot press machine then applies heat and pressure to the assembly, activating the adhesive and bonding the melamine paper to the substrate. The fast cycle time of the machine ensures quick production turnaround without compromising on quality. By mastering the art of laminating melamine paper on MDF, particle board, and plywood using short cycle hot press machines, manufacturers can streamline their production processes and deliver superior finished products to their customers. In conclusion, the use of short cycle hot press machines for laminating melamine paper onto MDF, particle board, and plywood offers a fast and efficient solution for manufacturers looking to enhance their production capabilities. By understanding the process and intricacies involved, businesses can achieve consistent and high-quality results that meet the demands of the market.
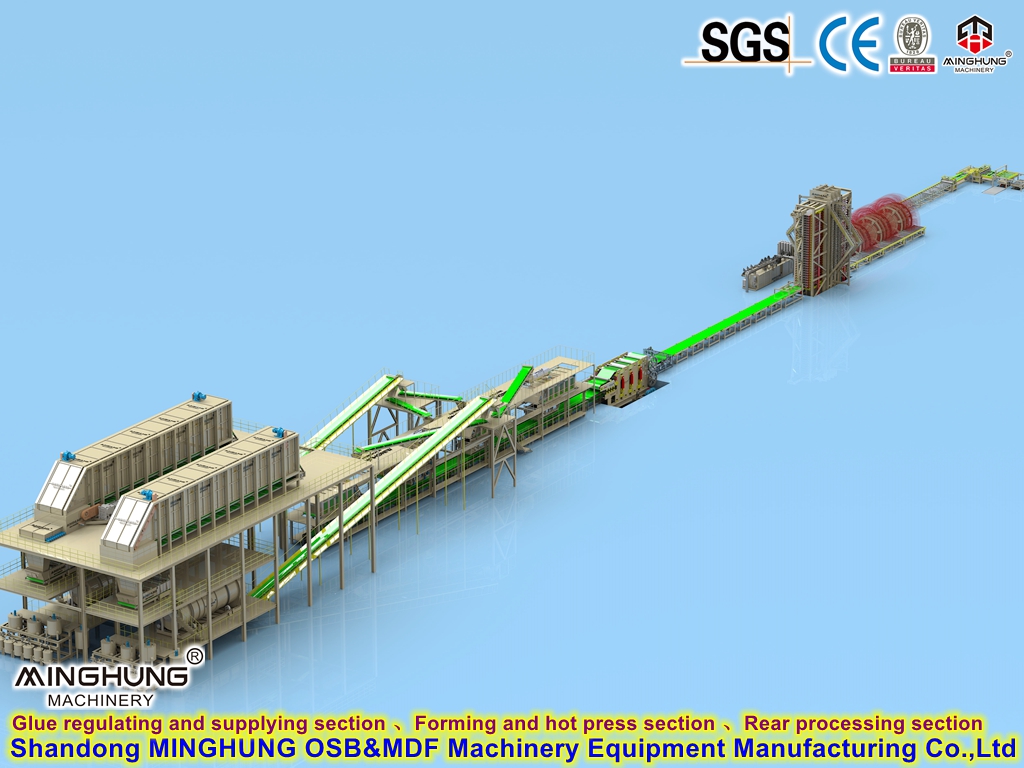
Boosting Productivity: Oriented Strand Board Production Line for Various Capacities Introduction: The demand for oriented strand board (OSB) has been on the rise in recent years, owing to its versatility and cost-effectiveness. To meet this demand, manufacturers have been investing in advanced production lines capable of producing different capacities of OSB. In this article, we will explore the Oriented Strand Board Production Line and its various capacities, ranging from 30,000m³ to 250,000m³ per year. 30,000m³ Capacity: The Oriented Strand Board Production Line with a capacity of 30,000m³ per year is an ideal choice for small to medium-sized manufacturers. This line is designed to optimize efficiency while maintaining a high-quality end product. With advanced automation and precision cutting technology, it ensures consistent board thickness and dimensional accuracy. Additionally, the line incorporates energy-saving features, reducing operational costs and environmental impact. 50,000m³ Capacity: For manufacturers looking to scale up their production, the Oriented Strand Board Production Line with a capacity of 50,000m³ per year is a suitable option. This line offers increased throughput without compromising on quality. Equipped with advanced resin blending and spreading systems, it ensures optimal resin distribution, resulting in improved board strength and durability. The line also incorporates advanced moisture control mechanisms, minimizing the risk of warping or delamination. 100,000m³ Capacity: With a capacity of 100,000m³ per year, the Oriented Strand Board Production Line caters to medium to large-scale manufacturers. This line is designed to handle higher production volumes while maintaining consistent quality standards. It features advanced mat forming technology, ensuring uniform strand orientation and adhesive distribution. The line also incorporates automated stacking and packaging systems, streamlining the production process and reducing labor requirements. 150,000m³ Capacity: The Oriented Strand Board Production Line with a capacity of 150,000m³ per year is tailored for manufacturers with substantial production needs. This line offers enhanced productivity through its high-speed continuous press system, capable of producing boards at a rapid pace. It incorporates advanced resin curing technology, ensuring optimal bonding strength and moisture resistance. The line also features automated quality control systems, minimizing the risk of defects and ensuring consistent product quality. 250,000m³ Capacity: For manufacturers with large-scale production requirements, the Oriented Strand Board Production Line with a capacity of 250,000m³ per year is the ultimate solution. This line is equipped with state-of-the-art machinery and automation systems, enabling efficient production at an unprecedented scale. It incorporates advanced moisture content monitoring and control systems, ensuring the production of high-quality boards with minimal wastage. The line also features comprehensive safety measures and maintenance protocols to ensure uninterrupted operation. Conclusion: The Oriented Strand Board Production Line offers a range of capacities to meet the diverse needs of manufacturers. Whether it s a small-scale operation or a large-scale production facility, there is a suitable line available. By investing in these advanced production lines, manufacturers can boost productivity, improve product quality, and stay competitive in the growing OSB market.
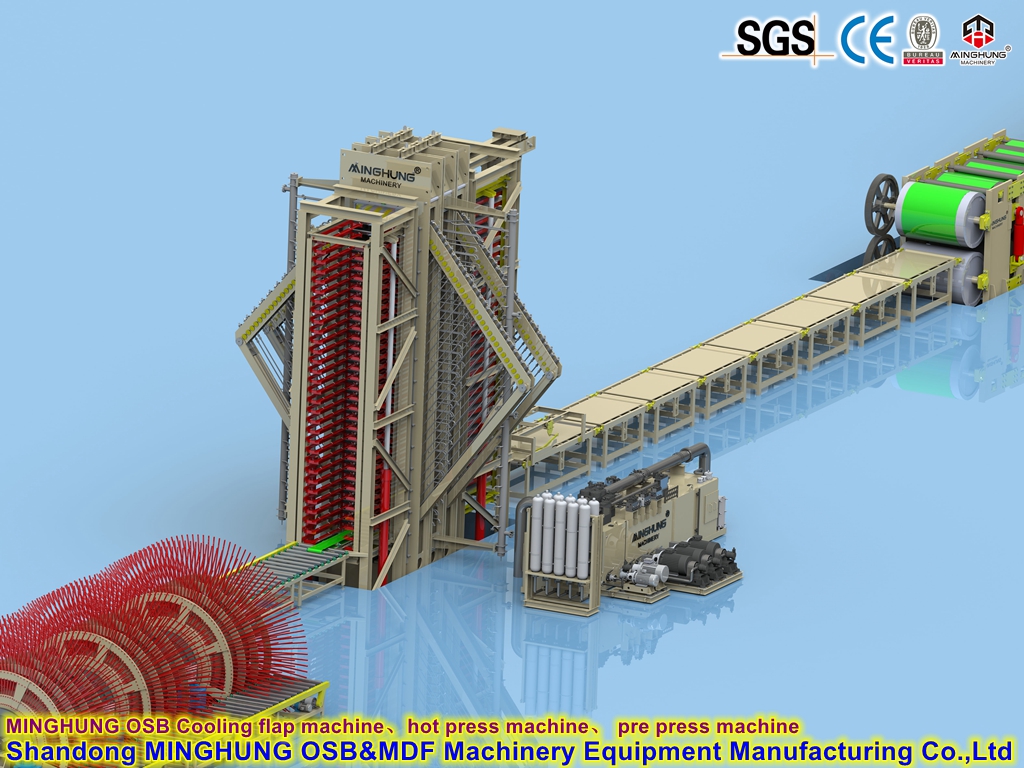
Particle Board Production Line: Meeting Your Production Needs Particle board, also known as chipboard, is a versatile and cost-effective material widely used in the construction and furniture industries. With its increasing demand, having a reliable and efficient particle board production line is crucial for manufacturers. In this article, we will explore the different annual output capacities of particle board production lines and the raw materials that can be used to produce various types of particle boards. Annual Output Capacities Particle board production lines come in various capacities to meet different production needs. The most common capacities include 30,000 cubic meters, 50,000 cubic meters, 100,000 cubic meters, 150,000 cubic meters, 180,000 cubic meters, and 250,000 cubic meters per year. These production lines are designed to ensure high-quality output while maximizing efficiency and productivity. 30,000 Cubic Meters Annual Output A particle board production line with an annual output of 30,000 cubic meters is suitable for small to medium-scale manufacturers. This capacity allows for a steady production flow while maintaining cost-effectiveness. It is an ideal choice for those starting in the particle board manufacturing industry or for businesses with limited space and resources. 50,000 Cubic Meters Annual Output For manufacturers looking to expand their production capabilities, a particle board production line with an annual output of 50,000 cubic meters is a suitable choice. This capacity offers increased productivity and allows for larger production volumes. It is an excellent option for businesses experiencing growth and higher demand for particle boards. 100,000 Cubic Meters Annual Output A particle board production line with an annual output of 100,000 cubic meters is designed for medium to large-scale manufacturers. This capacity provides a significant boost in production capabilities, allowing manufacturers to meet higher demand and expand their market reach. It is an ideal choice for businesses aiming to increase their market share and establish themselves as key players in the industry. 150,000 Cubic Meters Annual Output Manufacturers with even greater production needs can opt for a particle board production line with an annual output of 150,000 cubic meters. This capacity offers a substantial increase in production volume, enabling manufacturers to cater to a larger customer base and fulfill bulk orders efficiently. It is a suitable choice for businesses experiencing rapid growth and aiming to become industry leaders. 180,000 Cubic Meters Annual Output For manufacturers with extensive production requirements, a particle board production line with an annual output of 180,000 cubic meters is an excellent investment. This capacity ensures a high level of productivity and efficiency, allowing manufacturers to meet demanding market needs and maintain a competitive edge. It is an ideal choice for large-scale manufacturers or those operating in regions with high particle board demand. 250,000 Cubic Meters Annual Output The highest capacity available in particle board production lines is an annual output of 250,000 cubic meters. This capacity is suitable for manufacturers with substantial production requirements and a strong market presence. It allows for maximum productivity and efficiency, enabling manufacturers to dominate the market and cater to a wide range of customers. Raw Materials for Particle Board Production Particle boards can be produced using various raw materials, each offering unique characteristics and applications. Some commonly used raw materials include: - Poplar: Poplar particle boards are lightweight and have good dimensional stability, making them suitable for furniture and interior applications. - Pine: Pine particle boards are known for their strength and durability, making them ideal for structural and load-bearing applications. - Birch: Birch particle boards offer excellent strength and resistance to moisture, making the
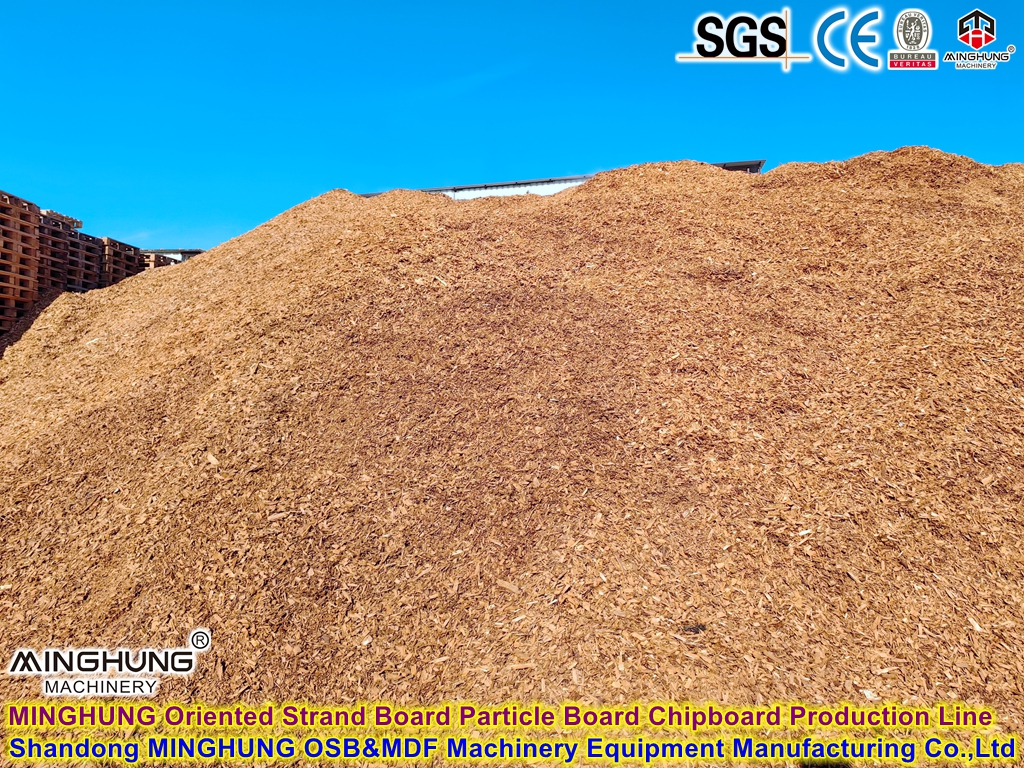
Enhancing Efficiency with Automated Saw Lines for Wood-Based Panels Wood-based panels such as Oriented Strand Board (OSB), Medium Density Fiberboard (MDF), and Particle Board/Chipboard play a crucial role in the construction and furniture industries. To meet the growing demand for these materials, manufacturers are turning to automated saw lines for increased efficiency and productivity. Automated saw lines offer a range of benefits for producing OSB, MDF, and Particle Board/Chipboard. These advanced systems are designed to streamline the cutting process, ensuring precision and consistency in the final product. By automating the cutting process, manufacturers can significantly reduce waste and optimize material usage, leading to cost savings and improved sustainability. One of the key advantages of automated saw lines is their ability to handle large volumes of raw materials with minimal human intervention. These systems are equipped with advanced sensors and computerized controls that can detect imperfections in the wood and adjust cutting parameters accordingly. This results in higher quality end products that meet the strict industry standards. In the case of OSB, automated saw lines are essential for cutting the wood strands to the required dimensions before they are oriented and compressed into panels. The precision and speed of automated cutting ensure that each panel meets the desired strength and dimensional stability. Similarly, in the production of MDF, automated saw lines play a crucial role in cutting the fibers and resin mixture into boards of various thicknesses. The accuracy of the cutting process is essential for achieving the desired density and uniformity in the final MDF panels. For Particle Board/Chipboard manufacturing, automated saw lines are used to cut the wood particles and adhesive mixture into panels of different sizes and shapes. The efficiency of automated cutting ensures that each panel is consistent in thickness and density, meeting the requirements of diverse applications in the furniture and construction industries. Overall, automated saw lines for OSB, MDF, and Particle Board/Chipboard are revolutionizing the wood-based panel manufacturing industry. By incorporating advanced technology and automation into the cutting process, manufacturers can enhance efficiency, improve product quality, and stay competitive in the market. As the demand for sustainable and high-quality wood-based panels continues to rise, automated saw lines will play a vital role in meeting these evolving industry needs.
No represented companies found.
The company has no registered brand information.