Company Name | Contact Info | Location | ||||||||||||
---|---|---|---|---|---|---|---|---|---|---|---|---|---|---|
BRUKS KLOECKNER GMBH
Grabenstr. 1 DE-57647 Hirtscheid / / / GERMANY
|
Contact Info: +49 2661 28156
|
Hall: 6
Stand: 615 B
|
||||||||||||
Product Groups | ||||||||||||||
|
- Company Info
- Products
- Represented Companies
- Company Brands
Bruks Siwertell is a market-leading supplier of dry bulk handling and wood processing systems. With thousands of installations worldwide, our machines handle your raw materials from forests, fields, quarries and mines, maintaining critical supply lines for manufacturers, mills, power plants and ports. We design, produce and deliver systems for loading, unloading, conveying, storing, and stacking and reclaiming dry bulk materials, alongside equipment for chipping, screening, milling and processing wood for the biofuel, board, saw mill, pulp and paper industries. We are global and local. You will find our main offices in the US, Sweden, Germany, China, Philippines, and Taiwan, supported by a dedicated network of hundreds of representatives and dealers worldwide.
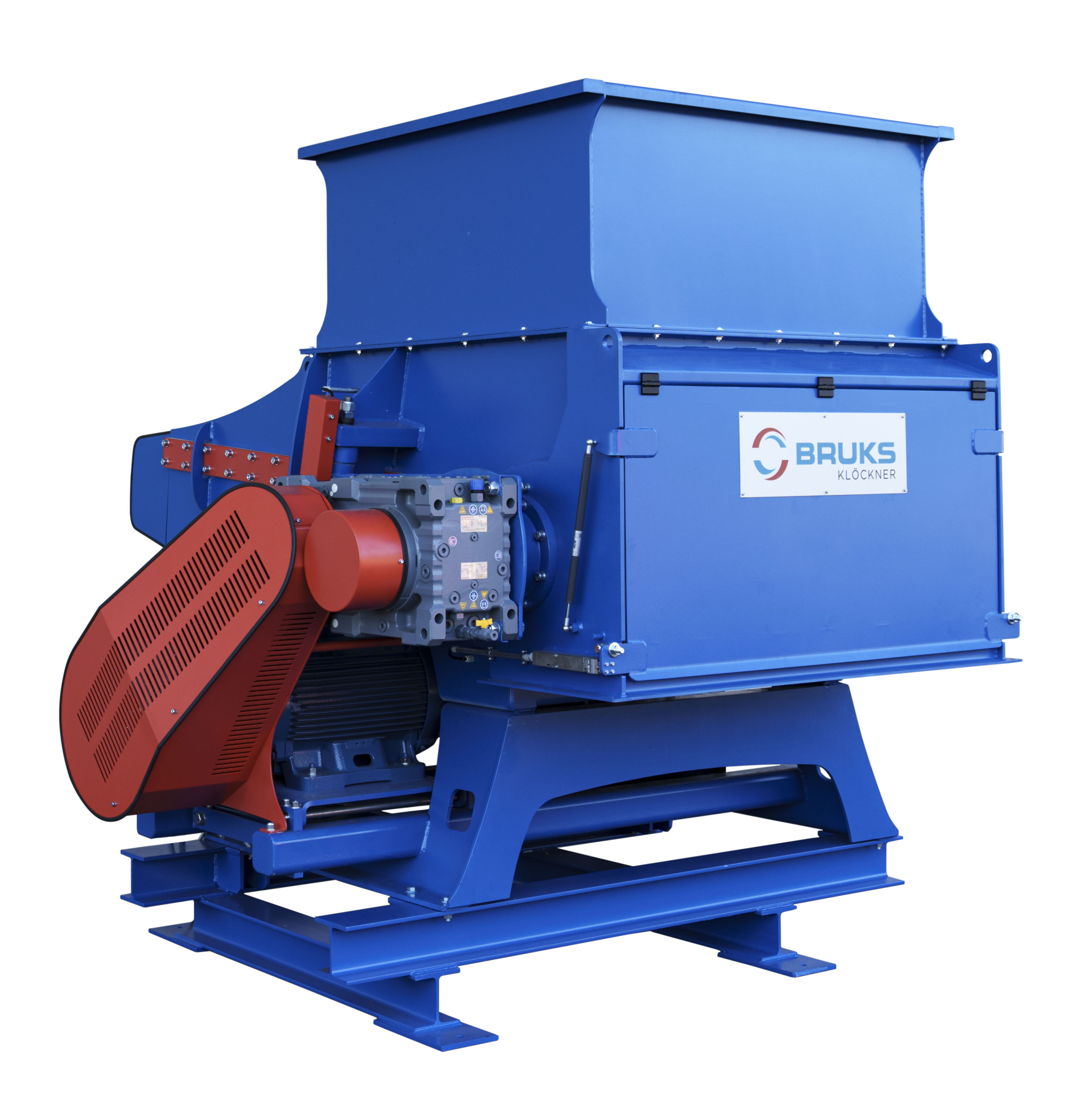
Wood waste processing equipment, such as the Bruks Klöckner residue upgrader RU 14-4, is key for converting wood processing residues into valuable fiber. Our RU 14-4 wood waste processing equipment is capable of performing a wide variety of wood residue processing tasks. The RU 14-4 s outstanding features include its robust construction, high efficiency and the reliable production of consistent quality wood chips from varying feedstocks. The RU 14-4 specialized wood waste processing equipment is ideal for use across a wide range of applications including the pallet, panelboard and furniture industries, sawmills, carpentry businesses and wood fiber-packaging manufacturing. It ensures that any end-of-life timber is not wasted, but repurposed, maximizing the profitability of an operation and also its sustainability. The RU 14-4 upgrades waste or end-of-life timber to deliver wood chips that can be used across a number of industrial applications, for example, in the bioenergy market. Input material can include a wide range of wood processing residues pallets, particleboard, hard and soft wood waste, bark, medium-density fiberboard (MDF) and oriented strand board (OSB). WHOLE PALLETS HANDLED WITH EASE The RU 14-4 has a wide-diameter hopper, which can accommodate large off-cuts, logs, and all common pallet sizes, including single-use types. Our RU 14-4 wood waste processing equipment can withstand smaller-sized extraneous material due to the rotation speeds of the rotor and the geometry of the knives. This means that complete pallets, including packaging items, nails, screws and metal fittings can be shredded. In cases of excessive extraneous material, the machine will automatically stop to avoid damage. HEAVY-DUTY PERFORMANCE Material is delivered into the unit via a powerful, hydraulically operated pusher with optimized geometry. The pusher is guided by large rollers and its action is dependent on the load entering the machine. Both the machine and its pusher floor make use of reinforced Hardox material, making it extremely durable. The number and size of the cutting tools, as well as the screen perforations, are dimensioned according to operational requirements and the type of input material handled. The RU 14-4 wood waste processing equipment housing features a user-friendly design, allowing for quick and easy control, including the rotation of cutting tools, counter-knives and screens. DESIGNED FOR MINIMIZED MAINTENANCE Maintenance costs are minimized through good design and the quality of components, including the wear-resistant steel cutting tool, which can be rotated to even wear patterns and maximize use. Operational advantages Flexible configurations for different operational requirements Suitable for use in a wide variety of applications High throughput rate Consistent end-product regardless of input materials Suitable for wet and dry wood material handling Solid, quality construction Easily maintained Able to withstand smaller-sized extraneous material Wide range of input material accommodated Pallets Particleboard Hard and soft wood waste Bark Medium-density fibreboard (MDF) panels Oriented strand board (OSB) Industrial applications Furniture industry Pallet industry Carpentry business Panelboard industry Sawmills Wood fiber-packaging industry
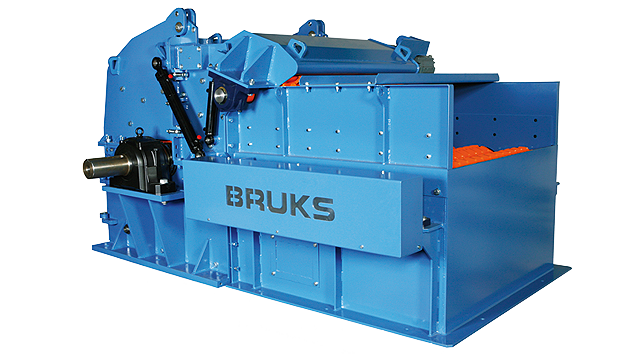
The Bruks Rotom hammer hog is an incredibly robust, reliable waste wood processing machine, offering a long service life even under high-use, demanding conditions. Hammer hog machinery components can be easily accessed for maintenance and can be turned to ensure maximum wear before replacement. It is also possible to tailor hammers and tips to individual waste wood processing applications. If an operator can benefit from natural forces, such as gravity, during manufacturing processes, this can be a valuable asset. Drop-fed wood waste-processing units, such as our Rotom hammer hogs, are no exception, and in addition to durability are highly energy efficient as well. Sharing many of the same proven design characteristics as its horizontal-fed counterpart, the drop-fed hammer hog unit is available in a range of standard sizes and is capable of processing wood waste up to a capacity of over 375 (standard) m³/h. Bruks Rotom hammer hog dropfed Drop-fed hammer hog units can easily process many different types of materials like bark, forest residues, industrial wood waste and sawmill waste. They have a compact, robust design, which is easy to service and maintain, and offer reliable performance.
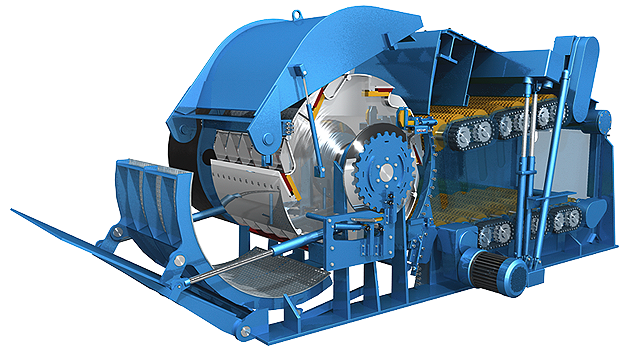
We manufacture complete chipping lines that meet the highest performance and reliability criteria. Our heavy-duty machinery can handle the toughest conditions and Bruks horizontal-fed drum chipper is no exception. Bruks Drum chipper horizontal Our drum chippers, with their large in-feed openings, lead the market and are capable of processing any waste wood product. Logs or bundles of wood with a diameter of over a meter can be reliably processed in Bruks larger chippers. With the ability to produce up to 300t/h of high-quality pulp mill chips, or smaller microchips for use in the biofuel industry, our drum chippers have flexible arrangements to produce even large chips of up to 200mm in length. With more than 50 years of experience and over 10,000 drum chippers installed, you can depend on a well-tested product that will deliver a long, economic life with low maintenance costs. Bruks Drum chipper horizontal WEAR RESISTANT, PROVEN TECHNOLOGY Our drum chippers have heavy-duty, self-aligning bearings that are centered in steel housings and bolted to the side walls of the machine. These deliver a long and effective service life. In addition, their feed rollers have special teeth that are surface-hardened by a heat treatment process, resulting in a particularly high wear resistance. We can deliver rollers with the option to have exchangeable wear segments. Hydraulic or pneumatic cylinders are used to regulate the pressure of the upper feed rollers and to open the upper feed rollers for maintenance and easy cleaning. Hydraulic cylinders are also used for maintenance functions and easy access for cleaning and knife change.
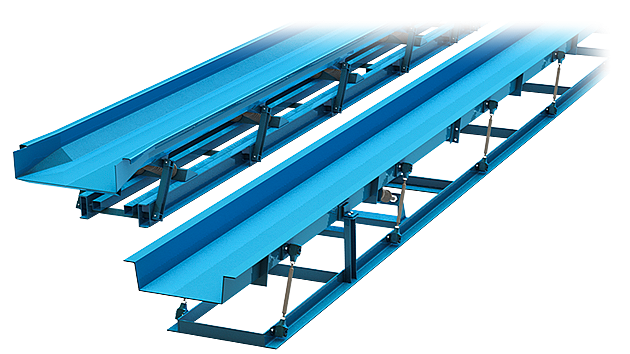
Our modular vibrating conveyors offer an extremely efficient, multi-functional method of conveying and processing different sized bulk materials, including larger and longer pieces of processed wood. Their design ensures consistently high conveying speeds even under high loads. Bruks vibrating conveyor Vibrating conveyors can form part of complex processing facilities and are easily customized to meet varying needs. They are ideally paired with our Bruks screening systems. Integral screens are often incorporated into a conveying system and can efficiently separate over-sized or fine particles during material transfer. In some cases they eliminate the need for separate screening units entirely. Vibrating conveyors are particularly popular for use with horizontal drum chippers and can be specified for use with gravity-fed versions. They can also be fitted with a built-in metal detector or heating rods for operation in extremely cold environments. Bruks vibrating conveyor vibor screen LONG AND SHORT WOOD HANDLED WITH EASE Most often used in sawmills, pulp and board mills as well as in bio-fuel applications, Bruks vibrating conveyors are available in a light, medium and heavy-duty design. They can easily accommodate long and short wood such as logs, slabs, edgings, trim-ends, chips, sawdust and bark, and can transport materials in parallel without mixing them. TAILORED FOR EACH APPLICATION Vibrating conveyors are tailored for each application to deliver the best possible operational performance. vibrating conveyor bruks siwertell Guide fins in the trough bottom help to orient material so that short wood waste, for example, has a better chance of being chipped properly, improving chip quality. Infeed conveyors can be equipped with a capacity control that reacts to the chipper s motor load. MINIMAL MAINTENANCE REQUIREMENTS Vibrating conveyors require very little maintenance. Their troughs are supported by springs that vibrate as a result of a crank shaft with single or multiple connecting rods. These steel or fiber-glass springs provide a long service life and low maintenance requirements. They also have flexible, tough attachments for smooth starts and stops. The simple operation of these conveyors provides a smooth, leveled-out material distribution due to the vibrations. Material enters the conveyor and spreads evenly without high-impact forces. Balanced and unbalanced designs are available, depending on cost and foundation requirements. A robust, concrete foundation or on-board counterweight balances the dynamic forces generated by the vibrating equipment.
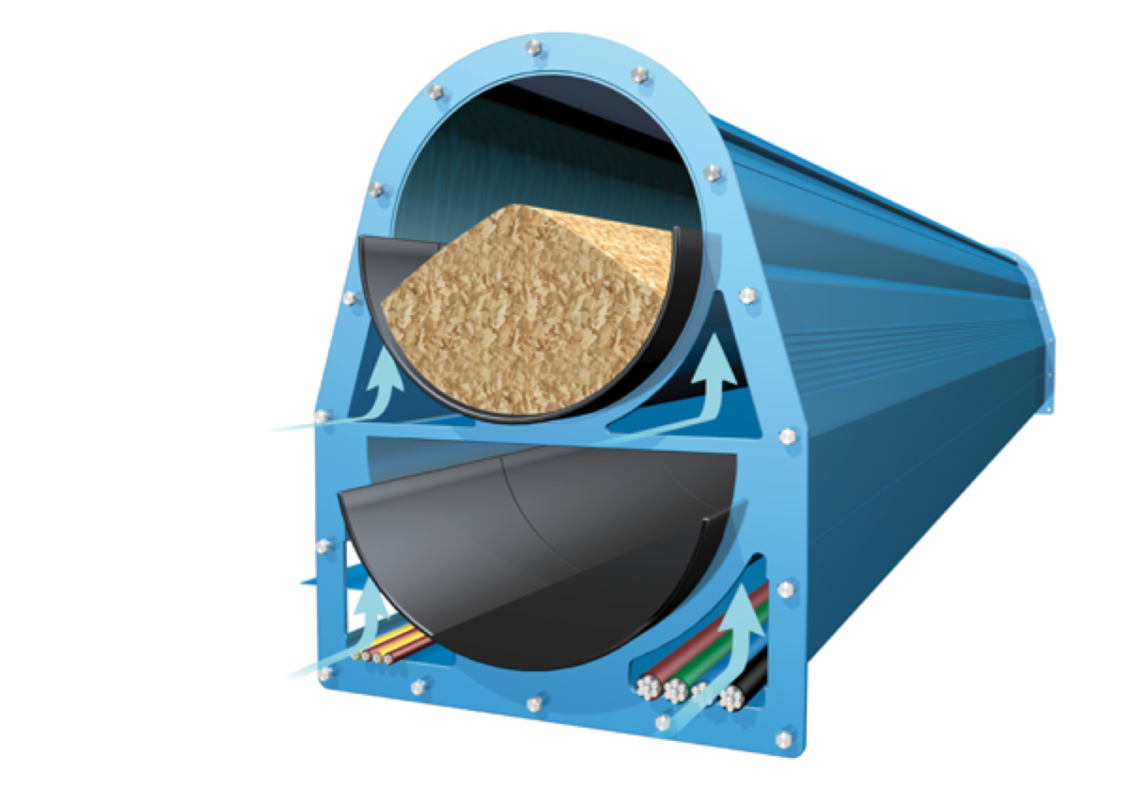
This is why we have developed conveying systems that use air-cushion technology, as well as offering our time-tested idler belt and drag chain conveyors. Our innovative air-supported conveyor range includes the Tubulator and The belt conveyor .In addition to offering some of the most performance-proven conveying technology on the market, Bruks Siwertell continuously looks to enhance and develop its conveying systems to ensure that it always delivers an effective solution that maximizes efficiency and economically suits an operator s needs. Although the air-delivery system and operating profile is different for both conveyors, they each capitalize on the benefits of low-friction conveying, delivering reduced operating and maintenance costs, with zero dust emissions and minimal material losses.
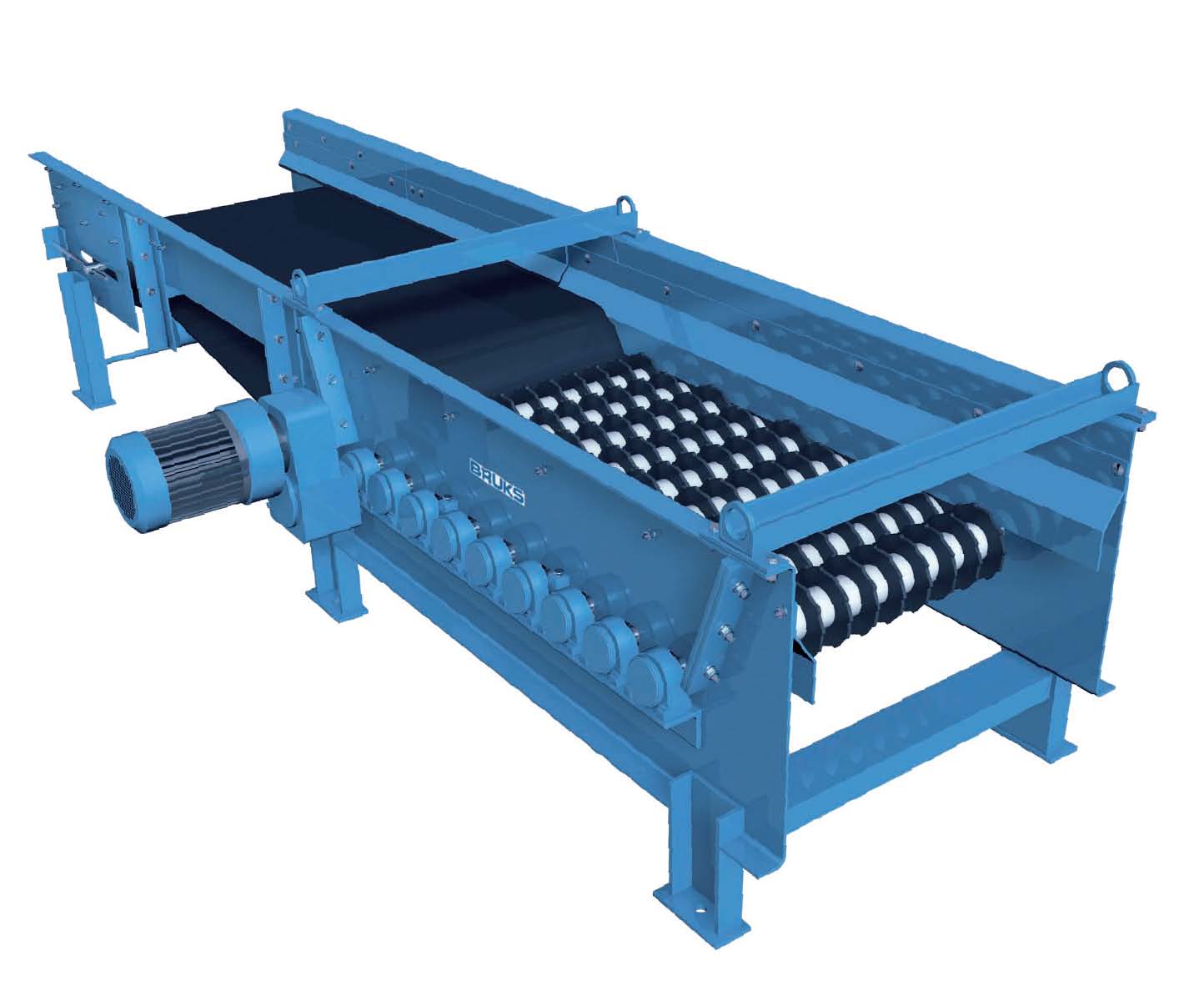
Screening and screening machines are a vital component in bulk material handling and wood processing. Screening equipment ensures a consistent size and quality in end products and removes fines and other unwanted pieces from the wood chip supply chain, making onward processing more efficient. SCREENING MACHINERY ENHANCES MANUFACTURING EFFICIENCY Bruks Siwertell offers a number of screening options depending on processing needs. By ensuring that oversized pieces are separated from a load, or during the process of manufacture, our screening systems can eliminate material handling problems and any unnecessary downstream damage or inefficiency to wood-processing equipment or other machinery. Our effective screening equipment maximizes a wood-processing plant s yield by minimizing losses and optimizing production efficiency. This includes our widely used vibratory screening equipment. SHAKING THE WASTE FROM THE LOAD Vibratory screening machines actively sort wood particles as they are conveyed onto a vibrating deck. This has a mesh base with pre-determined screen perforations. As this base vibrates, wood particles fall through the perforations. They are either the desired end product, or are the unwanted wood fractions that can be used for other purposes. For example, sawdust can easily be sifted from other wood products, like wood chips, and can then be collected for use in the production of compressed biomass wood pellets for the renewable energy market. The speed at which overs, both over-thick or over-sized fractions, can be separated from fines, such as sawdust, is critical in dictating the overall efficiency of production. In wood-processing facilities, overs can be fed back into a rechipper, for example, until the desired wood fraction size or thickness is achieved. Our screening machinery often acts as a pre-sorting process to speed up and efficiently remove sawdust from wood fractions. Screening machinery is an essential element in ensuring that every part of a tree can be effectively used, with screening equipment associated with almost every stage of processing until the final product is achieved or manufactured. An effective screening machine ensures that unwanted particles are separated quickly, and with minimal interference with the throughput of the rest of the feedstock. This time-saving effect is compounded where larger fragments must be recirculated several times, adding cumulative efficiency to mill processes. ROBUST SCREENING EQUIPMENT WITHSTANDS ABRASIVE BULKS In dry bulk processing, screening is equally important, again separating unwanted powdery fines from cargoes such as aggregates. These screening systems also have to offer heavy-duty, robust meshes and perforated screens, able to withstand the highly abrasive properties of some dry bulks. Our vibratory screening equipment and screening machinery has been designed to be extremely cost effective, require minimal maintenance and rapidly speed up the classification and sorting processes, which are essential elements in wood-processing plants and dry bulk material handling. MINIMAL MAINTENANCE, LOW OPERATING COSTS AND DECADES OF RELIABLE SERVICE Minimal maintenance and maximum equipment availability are delivered through robust, quality components, and the fact that a screening machine, such as vibratory screening equipment, is not exposed to significant forces. This means minimal wear and tear, low operating costs and decades of reliable service. Bruks Siwertell s screening solutions can be supplied as standalone units or, for larger processing facilities, can be supplied as integral parts of the manufacturing machinery.
No represented companies found.
The company has no registered brand information.